Industry Activities
The Award-winning Automotive Fasteners by JINGFONG
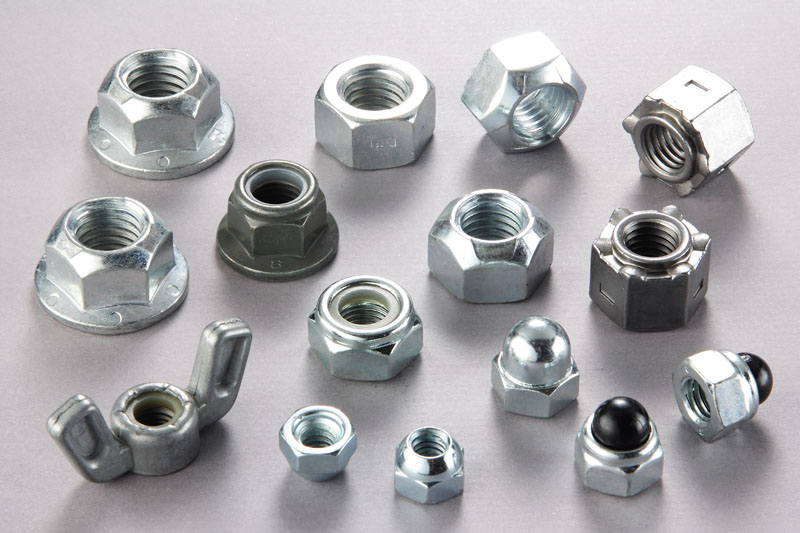

Add to my favorite
2020-05-19
JingFong Industry Co., Ltd. is Taiwan’s first lock nuts factory. Nowadays it has become a company with the annual production of 25,000 tons and the revenue of US$ 45 million. Focusing on the high-end automotive fastener market, JingFong mainly supplies products to European and American car manufacturers and plays a significant T1/T2 supplier in the supply chain. It mass-produces high precision parts with cold forging manufacturing procedures (including forming, threading, pressing and surface treatments) and has critical technology and takes good control of lead time and quality, all of which help achieve efficient management and monitoring.
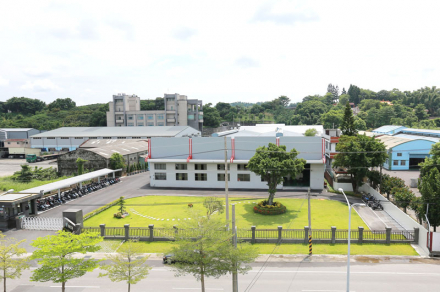
Impressive R&D Capability and Award-winning Products
JingFong’s automotive fasteners produced for the assembly of “Daimler’s passenger cars” and “ZF Sachs’ shock absorber valve” have been both honored with Taiwan Excellence Award this year. “The core competence of JingFong is based on our know-how and R&D capabilities. We implement force analyses with a simulation software to ensure the highest accuracy of mechanical properties and performance during the development phase of products,” says the Company’s owner. JingFong has been aggressively introducing the quality alert and forging force analysis tool, providing high-quality manufacturing procedures and quickly analyzing causes of defective products to speed up the adjustments in manufacturing procedures.
JingFong is currently able to deliver products within 60-75 days, faster than its competitors’ average 90 days standard. It is also taking many steps to achieve the 0 PPM quality standard, which include requiring complete test results in the phase of material selection, building up a mechanism to monitor quality, carrying out full-inspection with automatic optical inspection machines, and integrating the workforce to do double-checks.
Seizing the Chance of Upgrading Equipment and Facilities
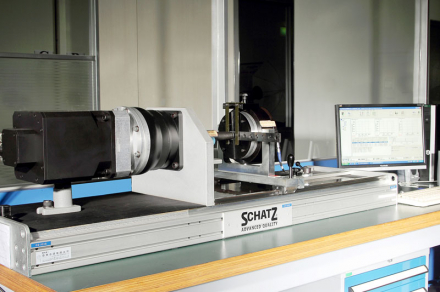
Although the Covid-19 pandemic has given a really hard time to the automotive market, JingFong still seizes the chance of expanding its current facilities and upgrading to smart manufacturing including IoT, viewable quality, quality monitoring, forging force analysis, and IT upgrade. JingFong expects to complete the upgrade to smart manufacturing lines within 6 months, which is estimated to enhance the ratio of machine utilization by 30%, reduce the time of machine breakdown without warning by 30%, shorten the lead time to 60-70 days, and increase the manufacturing efficiency by 50%. JingFong is taking actions to strengthen its know-how and upgrade production lines for further business transformation during the pandemic, hoping to reduce the impact to the minimum level, increase the ability to deliver products quickly when the order switching effect emerges, and maintain its technical power and quality level as the best response to the pandemic.
Accumulating Strengths to Face Future Changes in the Automotive Industry
JingFong thinks that there’ll be a drastic change in automotive fasteners with the development of electric vehicles and the trend of light-weighting will force manufacturers to use a large volume of Alu-Mg alloy fasteners to reduce the weight of a car. Noticing such a change, JingFong is now active in contacting EV assemblers, developing other metal forming procedures, working with customers in end-product design, manufacturing trial batches for accumulating technical strengths, in order to respond to the upcoming trend of product demand change.
JingFong and its Thailand branch have recently launched a 3-year capacity increasing plan, which includes the expansion of factories & addition of equipment for forming, tapping, locking and assembling, and the introduction of a new surface treatment line. According to the 3-year plan, JingFong will invest NT$ 0.5 billion in expanding factories (scheduled to be completed by 2022). The total factory area will be increased by 15,195m2 and the total capacity will be increased by 1.5 times, not to mention that the newly added surface treatment line will make the entire process become more flexible and help reduce the cost and lead time. Combined with this year’s IoT-enabled machines & IT upgrade plan for smart manufacturing, JingFong definitely will gain more competitive edge and promote its quality, lead time and profitability to a higher level.
E-mail: sales@jingfong.com.tw
璟鋒
車用扣件
得獎
JingFong
automotive fastener
award winning
扣件
國際展會
惠達雜誌
匯達實業
外銷媒合
廣告刊登
螺絲五金
五金工具
紧固件
台灣扣件展
印度新德里螺絲展
越南河內螺絲展
墨西哥瓜達拉哈拉螺絲展
美國拉斯維加斯螺絲暨機械設備展
波蘭克拉科夫螺絲展
義大利米蘭螺絲展
德國司徒加特螺絲展
wire Dusseldorf
FASTENER FAIR INDIA
FASTENER FAIR VIETNAM
FASTENER FAIR MEXICO
FASTENER POLAND
FASTENER FAIR ITALY
FASTENER FAIR GLOBAL
FASTENER WORLD
READ NEXT

Subscribe
