Industry Activities
ALL IN ONE: KSP12-R
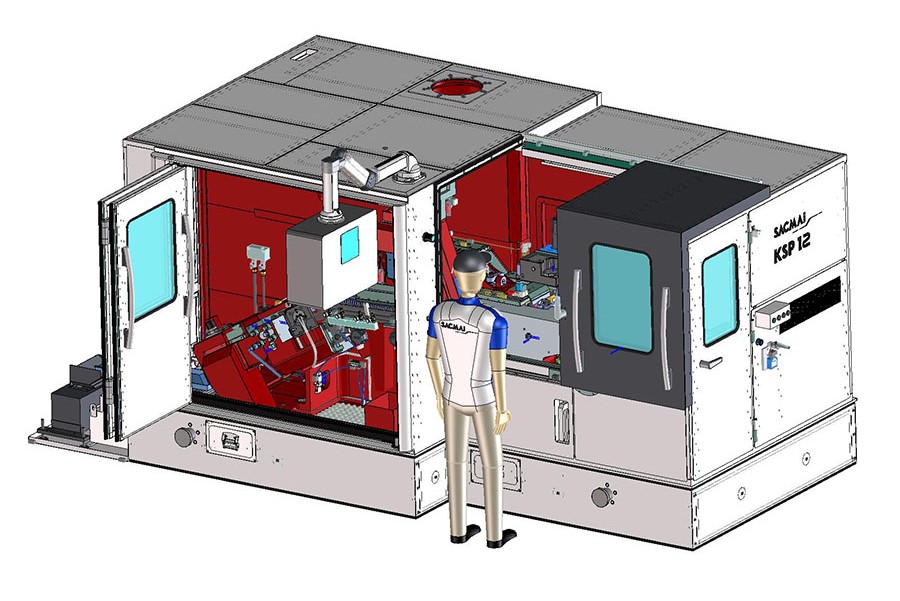

Add to my favorite
2021-11-26
Sacma World Premiere: New Double Blow Header model KSP12-R with threading unit.
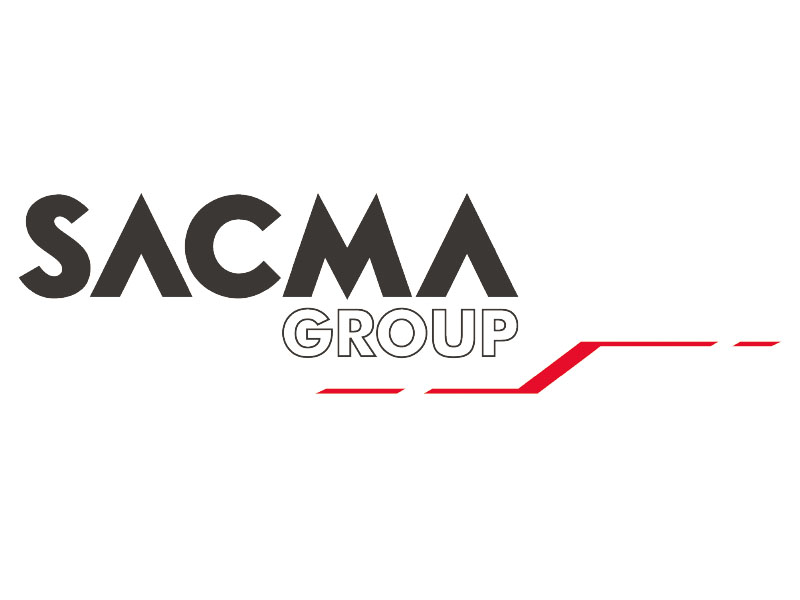
Sacma Group is well known for the designing and manufacturing of Combined Headers which are able to produce fasteners from M4 to M24.
These Combined Headers can produce finished parts like fasteners and screws for the automotive industry, starting from the wire and are the best solution for high productivity requirements, consolidation of production methods, floor space utilization and work flow in the fasteners manufacturing process by having the forming, pointing and thread rolling all in one machine.
To complete its whole range, Sacma is introducing the new combined header model KSP12-R to run fasteners that range from M3 to M8 with a maximum shaft length of 60 mm. The machine is a double blow header with an integrated threading station, representing the new generation of the worldwide known KSP11-R. Sacma is re-introducing in the product line the 1D2B combined header to face an increasing request of small and self-tapping screws widely used in different industry fields.
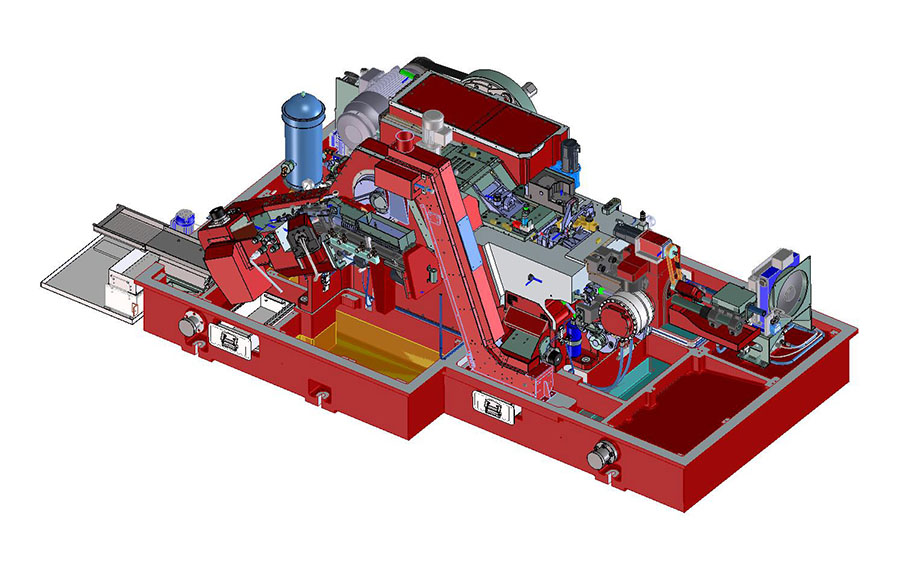
The KSP12-R combines typical SACMA solutions, proven by thousands of machines, with the most advanced mechatronic technology available in the market. The one-piece main frame, perlitic cast iron, normalized, natural aged for at least 12 months, high precision machined, is a guarantee of rigidity and stability for all machine life. Major set-up adjustments are now motorized for a quick and friendly changeover: S-feed wire feeder driven by a torque motor, motorized wire stock gauge and DKO, threading starter driven by torque motor with self-learning function.
The quality management is facilitated by two gates interfaced with the load monitoring system and discharging of NC parts, after the header and after the roller. An optional sophisticated load control system protects the machine against overloads and monitors the forming and rolling processes. Scraps separators in different sizes are available when producing self-tapping screws.
All these features make the KSP12-R the best value for the Customer’s investment, especially when running parts traditionally by a line of connected machines. This ALL-IN-ONE high productivity process allows to quickly return the customers investment. These legendary long life SACMA machines guarantees future profits thanks to the following concept:
VS production floor / sqm: the relation between the floor utilized by a 1D2B combined header against a line of connected machines (1D2B header + conveyor + roller) is normally 1 to 3.
VS production floor / ppm: consequently, more parts produced per area make the overall plant more profitable and efficient.
VS manpower: one combined header requires one operator. More often one operator manages two or three small combined headers. In case of separate machines, only one operator is not enough to attend this many lines.
VS maintenance: more machines mean more maintenance. The Combined machine is only one machine that does two operations, therefore less maintenance is required.
VS changeover time: the total time to set up two different machines, with related feeding systems, is higher than the one of combined machine.
VS eco-friendly: having a Combined machine, with the header and threader enclosed in one soundproof enclosure, allows all of your coolant and oils to be recycled safely and controlled in one sealed area: no oil leakage, less pollution, clean and safe working place .
VS start up time: all Sacma machines are recognized as “quick plug in” equipment. The KSP12-R is ready just a few hours after the installation, and is quickly ready to start production. The advantage remains when necessary to update the factory layout. Only one machine needs to be fixed to the floor, and connected to the air plant and the power supply.
VS energy consumption: only one motor for two operations is more efficient than several motors. Combined headers consume less than two machines and the power monitoring becomes more simple and more convenient.
VS Tool life: the forged parts still warm and oiled are placed in the roller. Thanks to this, the flat dies last a lot longer, reducing the running costs and increasing the production efficiency.
The orders for this innovation have already started and the first machines will be delivered within 2021!
sacma
KSP-12
fastener machine
扣件
國際展會
惠達雜誌
匯達實業
外銷媒合
廣告刊登
螺絲五金
五金工具
紧固件
台灣扣件展
印度新德里螺絲展
越南河內螺絲展
墨西哥瓜達拉哈拉螺絲展
美國拉斯維加斯螺絲暨機械設備展
波蘭克拉科夫螺絲展
義大利米蘭螺絲展
德國司徒加特螺絲展
wire Dusseldorf
FASTENER FAIR INDIA
FASTENER FAIR VIETNAM
FASTENER FAIR MEXICO
FASTENER POLAND
FASTENER FAIR ITALY
FASTENER FAIR GLOBAL
FASTENER WORLD
READ NEXT

Subscribe
