Industry Activities
Hwa Hsing to Celebrate 50th Anniversary. President Chen Expounds His Business Philosophy
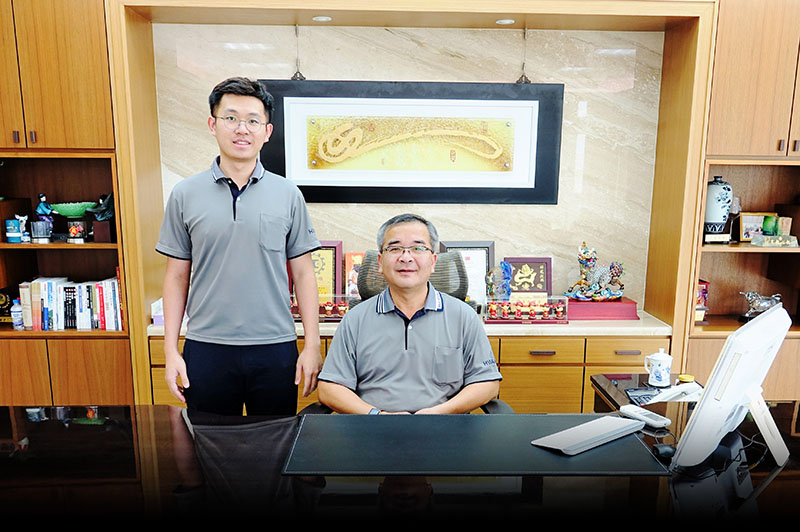

Add to my favorite
2022-09-20
The development of Taiwan fastener industry has been around 7-8 decades with the current number of local fastener businesses being nearly 2,000. However, Taiwan fastener businesses of over 50 years of history are rarely seen. Is it because of the lack of product manufacturing technology or the talent gap resulted from late succession?
On the contrary, leading construction & DIY screws manufacturer Hwa Hsing Screw Industry Co., Ltd. also facing the competition and challenges from the world continues to grasp opportunities to secure stable growth and is even about to reach its 50th anniversary in 2023. Its employee training and succeeding strategy, dedication to one-stop smart production lines and advantages it has demonstrated through product quality and customer service all play quite essential parts.
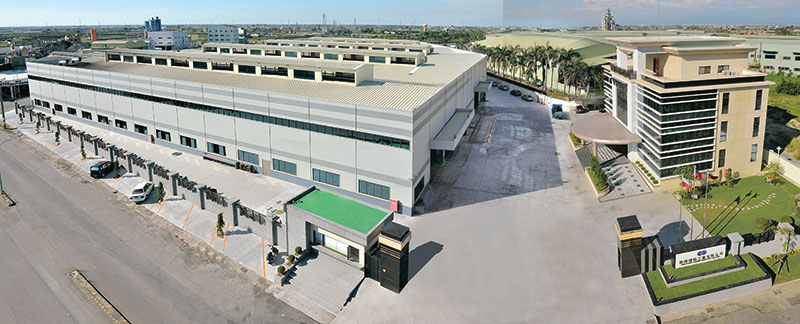
Selecting the Successor from Outside or Within the Company is a Priority to be Considered?
No! Technique Succession of Senior Technicians Matters the Most
Hwa Hsing President Jim C.N. Chen, who’s also a “2nd-generation fastener business runner”, knows deeply about what possible problems new industry successors may face. Over a decade ago, he experienced in person the era when the employees of Hwa Hsing’s China plant used to voluntarily work overtime and did whatever it took to learn more. However, with the change of industrial environment, young generation’s definition of “a company in which working load is high but still highly attractive to job seekers” has shown subtle change. Compared to the IT Industry with higher salaries and better reputation, traditional screw factories with a “sooty and messy” stereotype has not been the first priority choice for the young generation for the time being, but they are actually an unignorable force that supports Taiwan (aka. Kingdom of Fasteners) and pushes global industries forward. Accordingly, when the succession of Taiwan fastener industry continues and more young people come to work in the industry, he’s always thinking, what is the best way to achieve sustainable operation and simultaneously create more opportunities for the young fastener generation. Such a thought has been completely fulfilled in Hwa Hsing’s HR management strategy for years.
“When it comes to business succession, most people will focus on if the successor should be selected from outside the company or directly from within the family. This is pivotal, of course. However, I think the seamless succession of senior technicians’ technique is more important. Many businesses are talking about insufficient talent pool, but is this true? I once heard a fastener business in southern Taiwan whose employee turnover is almost 0 and whose senior employees are working with their sons in the same company. With this special relationship, teaching is more selfless, learning efficiency is greatly increased, and technique succession is more smooth. I personally admire such a way and would encourage senior employees to recommend their relatives to learn and work in Hwa Hsing,’ said President Chen.
After the 3rd generation started to work in Hwa Hsing, President Chen has gradually got out of the sales management circle and had much more time to care about employees. Fastener factories in early years might only hire 20-30 employees, nowadays, factories with 200-300 employees are already common. In the situation of more employees, various divisions, and complicated production lines, asking a newcomer to master all levels of technology and climb to the highest management position may take decades. Chen thinks that a technician doesn’t have to be capable of doing every thing, but he has to know much more than others do.” Chen also allowed his son to learn fastener threading and drilling after school, providing young people interested in working in traditional industries with a platform full of opportunities.
“Now is an era when the strong and the weak are determined based on their results. Although the workplace of traditional industries is not as comfortable as those of other industries, it can still be an attractive option for talents via giving rewards based on employees’ performance, suitable staff training, subsidies, and contractual incentives to offer employees more sense of achievement. As a result, with the decreasing birth rate, the fastener industry can still find, cultivate, and keep good talents.,” Chen added.
Smart Industry 4.0 Production Lines
Buildup of High Quality Service
In order to make technicians management more digitized and facilities/products/customer service more integrated, in recent years Hwa Hsing has dedicated to the setup of electroplating and heat treating lines, as well as suppliers platform, IoT equipment, and smart factory solutions for digitized production management and AI applications and consulted fastener professionals for setting up more suitable smart production lines. So far, it has reached the goal of real-time monitoring of daily output and higher capacity without changing labor deployment. Considering the possibility of sudden changes in order placements amid the pandemic, it has made early preparations for future challenges.
“Establishing Industry 4.0 production lines can help us do better jobs and facilitate communication between operators and machines. An Industry 4.0 production line that does not meet actual demand of fastener manufacturing has beset many fastener companies for so long, but with the guidance of experts familiar with the industry to conduct digital connection for ERP and the government’s program funds and subsidies to help us utilize the Big Data to manage staff/equipment or make decisions, we’ve made a big progress. On the other hand, the one-stop process also help us control costs, improve quality, and achieve punctual delivery, indirectly gaining more customer satisfaction and increasing brand awareness,” said Chen.
Valuing Factory Environment
Offering Service Fully Satisfying Customers’ Demand
BSCI and ISO 14000 certified Hwa Hsing is dedicated to creating a comfortable, safe, and environment-friendly workplace, hoping to attracting more young people to work in fastener factories. In addition to installation of solar panels and air-cons in some packaging units, last year it also replaced all smoke discharge devices on fastener machines with electrostatic systems in order to comply with stricter EP monitoring regulations in 5-10 years.
“We do whatever it takes to maintain a good environment. A few years ago we’ve adopted electrostatic systems in heat treatment lines, worked with our suppliers to redesign smoke discharge mechanisms, and asked our manufacturing equipment provider to directly install electrostatic smoke discharge devices onto the recently purchased machines, whose fully-confined outer cases can prevent smoke from dispersion, not to mention we even took out laser pens to inspect discharge. All of these not only make employees work harder, but also reveal our focus on corporate social responsibility,” said Chen.
Hwa Hsing delivers most of its products to European and U.S. markets, values collaboration with existing customers, and has lead times of most orders in hand controlled within 3 weeks. It has high supply capacity (3,000 tons/month) and shows strengths of low-volume-high-variety and satisfying urgent demand. A customer even contacted it to purchase 2 million boxes of pre-packed screws which had to be delivered within 2 months. Well-experienced Hwa Hsing not only found a packing box supplier in a short time, but also finished delivery within the required due date. Its good quality and punctuality greatly impressed the customer.
Industrial Interaction and Continuous Learning
Being once the Chairman of NCKU EMBA Alumni Association, President Chen values communication and experience succession of the fastener industry a lot and even held irregular communication events for NCKU alumni from the fastener industry. He encourages new fastener generation should upgrade themselves through different approaches and learn experience from communication with various industrial talents to widen personal networks and learn more distinguished management and marketing approaches, which will become essential resources for new fastener generation to succeed in the future.
Hwa Hsing contact: President Jim C.N. Chen
Email: jim@hwahsing.com
Hwa Hsing Screw Industry
technical succession
industry 4.0 production
environment-friendly workplace
華興工業
技術傳承
工業4.0生產
環境友善的工作環境
扣件
國際展會
惠達雜誌
匯達實業
外銷媒合
廣告刊登
螺絲五金
五金工具
紧固件
台灣扣件展
印度新德里螺絲展
越南河內螺絲展
墨西哥瓜達拉哈拉螺絲展
美國拉斯維加斯螺絲暨機械設備展
波蘭克拉科夫螺絲展
義大利米蘭螺絲展
德國司徒加特螺絲展
wire Dusseldorf
FASTENER FAIR INDIA
FASTENER FAIR VIETNAM
FASTENER FAIR MEXICO
FASTENER POLAND
FASTENER FAIR ITALY
FASTENER FAIR GLOBAL
FASTENER WORLD
READ NEXT
Industry Activities
2022-09-20

Subscribe
